Labs & Manufacturing
Jacam Catalyst has laboratories located throughout the United States in strategically located basins to provide our field engineers with faster analytical and performance data.
Laboratories
Jacam Catalyst has laboratories located throughout the United States in strategically located basins to provide our field engineers with faster analytical and performance data. With over 50,000 sq. ft. of lab space combined, we have state-of-the-art ICPs, GCs, scanning electron microscopes, dynamic scale loops, corrosion autoclaves, and many other specialized analytical and product performance test equipment. Jacam Catalyst is committed to being the leader in solving our customer’s complex problems. Jacam Catalyst’s laboratories are staffed with highly experienced chemists and technicians, and our research and development scientists are experts in all disciplines in oilfield chemistry. We employ a decentralized product development model where our scientific teams are strategically located to rapidly develop chemistries specific to area needs and provide performance testing to ensure products are performing as designed.
Full-service laboratories covering drilling, stimulation, production, pipeline, specialty chemicals, and R&D.
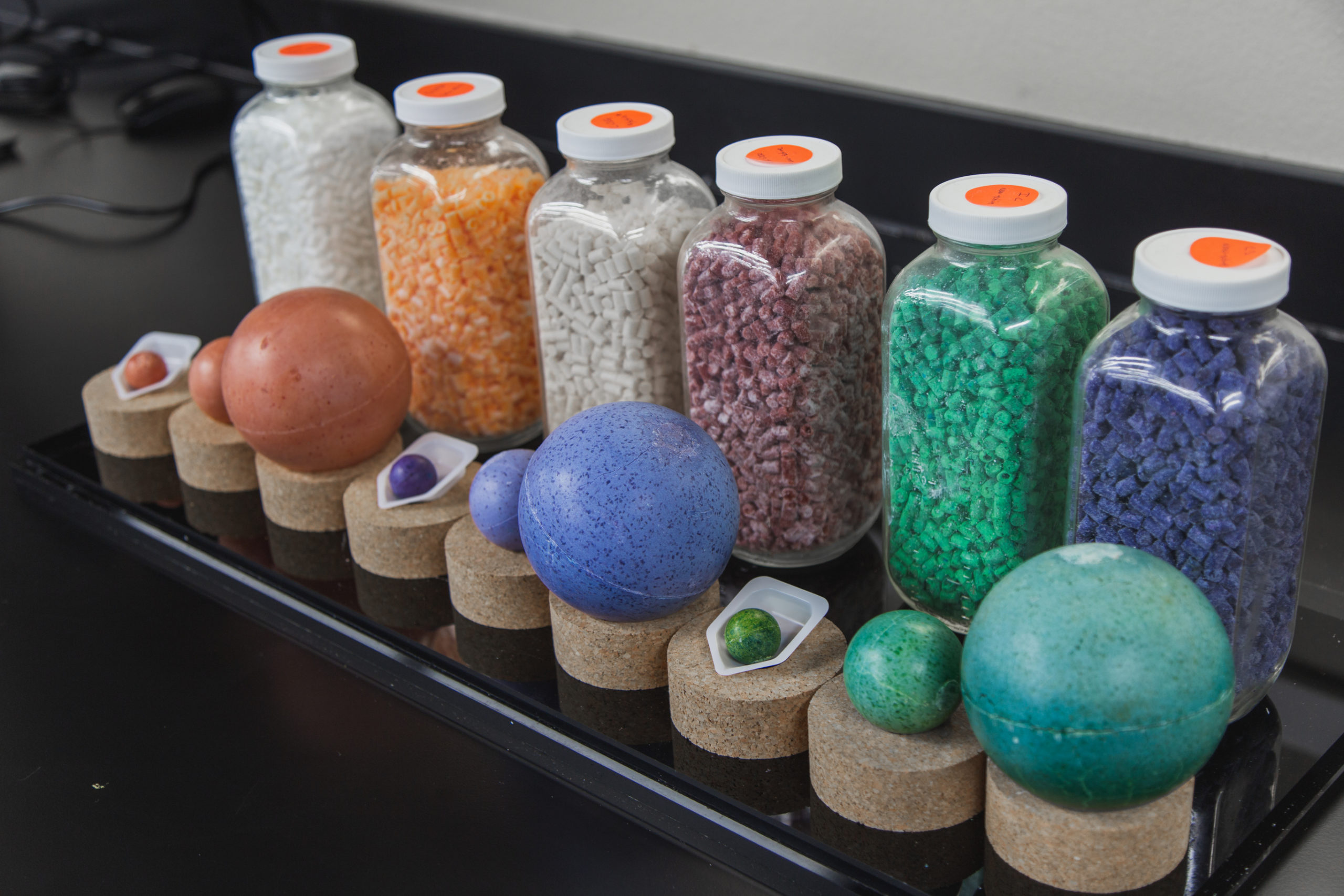
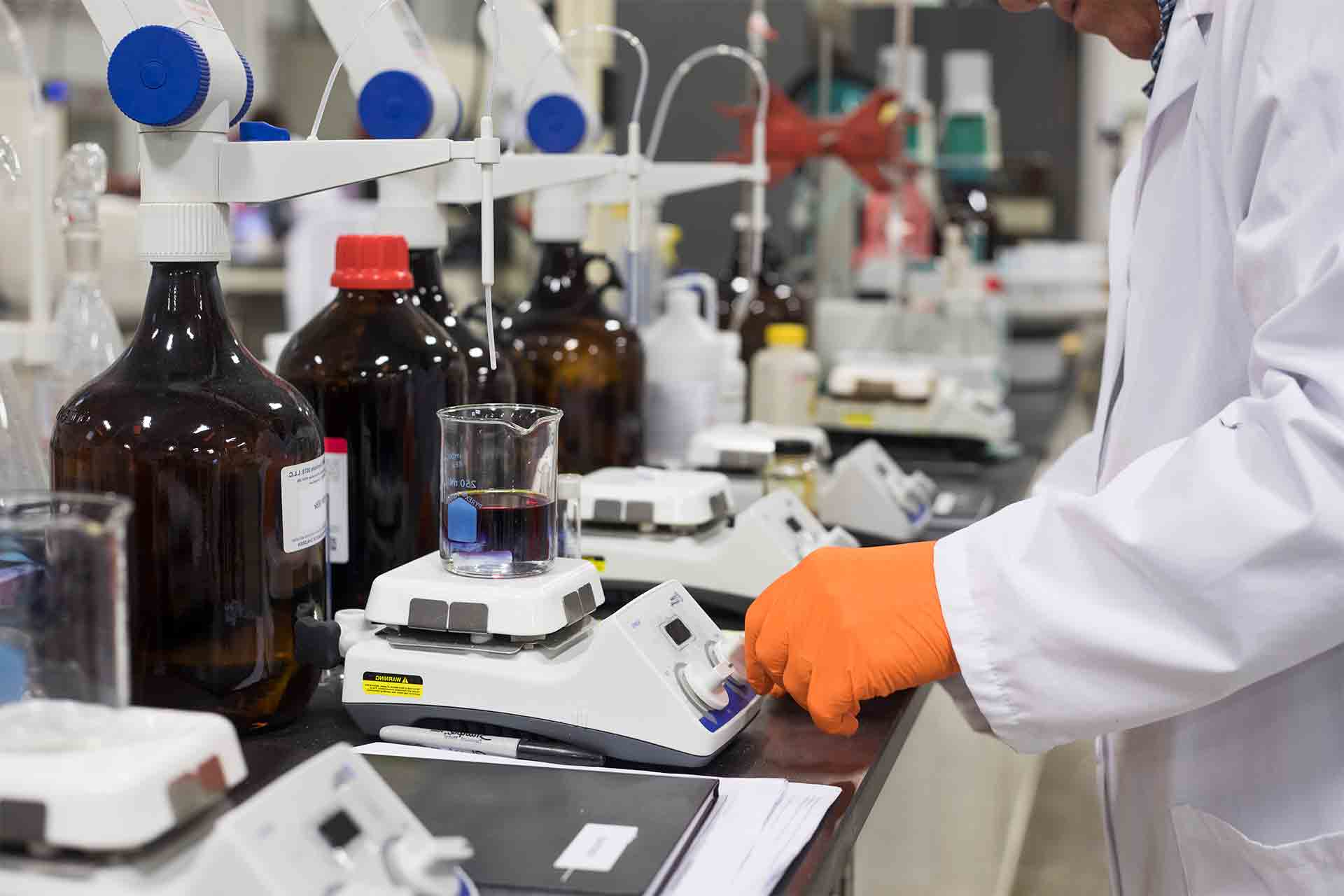
- Acid Stimulation
- Asphaltene Inhibitor Testing
- Bacteria Testing – ATP, Epifluorescence, Serial Dilution
- Corrosion Testing – Wheel, Static, RCE, HT/HP Autoclaves
- Corrosion Coupon Analysis
- Clay Swelling/Fines Migration Testing
- Emulsion Breaker Testing
- Failure Analysis
- Fluid and Solids Analysis
- Frac Flow Loop Testing
- Frac Fluid Load Recovery Testing
- Foamer/Defoamer Testing
- Gas/Liquid Residual Analysis
- H2S Breakthrough Testing
- Material Compatibility Testing
- Molecular Size and Composition
- Oil Analysis
- Paraffin Testing – Dispersant and Inhibitor
- Particle Size Analysis
- Pipe-On-Pipe Friction Testing
- Product Selection and Design
- Residuals Monitoring
- Scale Inhibitor Program Analysis
- Solid Determination/Analysis – Digestion, SEM-EDS, XRF, XRD
- Sulfur Analysis
- Surface/Interfacial Tension Testing
- Microwave Digestors
- Membrane Filtration Cells
- Metallographic Invert Microscope
- Muffle Furnaces
- Nuclear Magnetic Resonance Spectrometers (NMR)
- Optical Tensiometer
- Paraffin Flow Loop
- Pilot Scale Reaction Apparatus
- Pipe-On-Pipe Friction Apparatus – Linear and Rotational
- Refractometers
- Roller Ovens
- Scanning Electron Microscope – Energy Dispersive X-Ray Spectrometers (SEM-EDS)
- Stability Analyzers (Asphaltene) – Turbiscan
- Sulfur Analyzers (XRF)
- Turbidity Spectrometers
- UOP-163 Titration Apparatus
- UV-Vis Spectrometers
- Vacuum Ovens
- Water Clarification Cells
- X-Ray Diffraction Systems (XRD)
- X-Ray Fluorescence Spectrometers (XRF)
- Viscosity Analysis – Brookfield, HT/HP Grace 5600
- Water Analysis Reporting
- Water Quality Analysis
- Wax Analysis and PPD Testing
- Anaerobic Glove Boxes
- ATP – Luminultra, Hygenia Luminometers
- Automatic Titrators
- Brookfield Viscometers
- Capillary String Certification Apparatus
- Capillary Suction Test Apparatus (CST)
- Centrifuges
- Chandler 6500 Friction Flow Loops
- Cold Finger Apparatus – PSL
- Conductivity Meters
- Corrosion Wheel Testers
- Differential Scanning Calorimeters – DSC
- Dynamic Scale Loops (DSL)
- Epi-fluorescence Microscopes
- Fann 35A
- Flash Point Apparatus
- Fluorescence Spectrometers
- Force Tensiometers – Du Nouy Ring, Wilhelmy Plate
- FTIR Spectrometers
- Gas Chromatographs – Mass Spectrometer, Flame Ionization Detector (GC-MS, GC-FID)
- Grace 5600M HT/HP Viscometers
- High Pressure Liquid Chromatographs – Gel Permeation Chromatograph, Refractive Index Detector, Fluorescence Detector (HPLC-GPC/RID/FLD)
- HT/HP High Shear Corrosion Autoclaves (Rotating Cage, Rotating Cylinder)
- Incubator Ovens
- Inductively Coupled Plasma Spectrometers (ICP)
- Ion Chromatographs
- Laser Particle Size Analyzers
- Linear Polarization Resistance Corrosion Cells (Static, RCE)
- Liquid Chromatographs – Mass Spectrometer (LC-MS)
- Low Temperature Freezers (-40°F)
Manufacturing
Jacam Catalyst is a primary manufacturer of basic consumable chemicals, polymers, and minerals, which enables us to provide our clients with cost effective solutions. Our abundant formulation and blending capabilities allow timely fulfillment for drilling, stimulation, production, and pipeline chemicals.
- Products manufactured (low temp – 350°F to 400°F)
- Quats
- Amines
- Phosphate Esters
- Polymers
- Alkyl Ether Sulfates
- Betaines
- Alkanolamines
- Products manufactured (high temp – 400°F to 550°F)
- Imodazolines
- Phosphonates
- Resins
- Complex Esters/Demulsifiers
Kansas Facilities
-
- 160-acre facility
- 24 reaction vessels and 13 blend vessels across 10 buildings
- Products manufactured (low temp – 350°F to 400°F)
- Quats
- Amines
- Phosphate Esters
- Polymers
- Alkyl Ether Sulfates
- Betaines
- Alkanolamines
- Products manufactured (high temp – 400°F to 550°F)
- Imidazolines
- Phosphonates
- Resins
- Complex Esters/Demulsifiers
Midland Facilities
-
- 45-acre facility
- 19-active non-pressurized vessels –sizes range from 275 gallons to 6,700 gallons across 5 buildings
- Low temp reactions with heating and cooling capabilities
- 2-explosion proof facilities for oil soluble products
- Guar slurry mixing plant
- Dry-add system for delayed Crosslinker slurries
Capable of producing >50,000,000 pounds per month without additional equipment
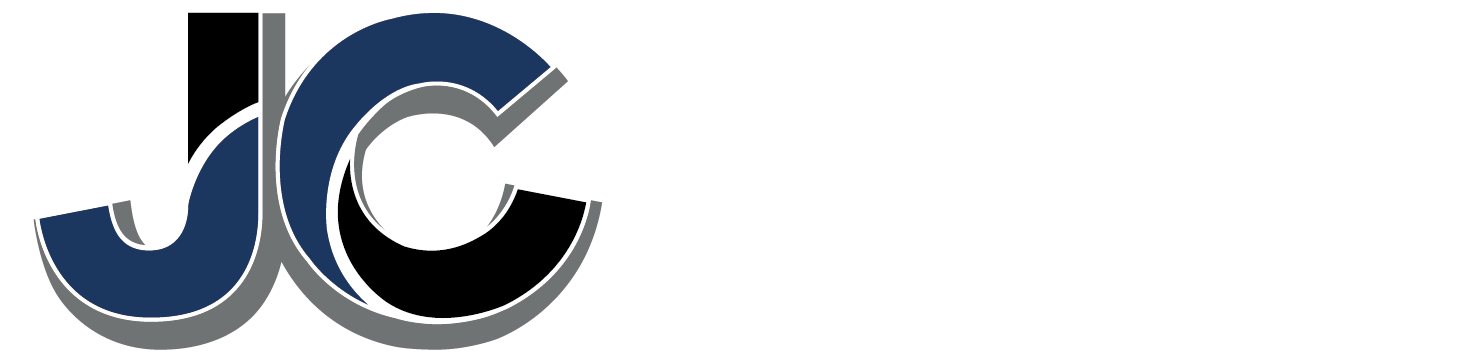
1,000+
Employees
50+
Locations
Headquarters
11999 East Highway 158
Gardendale, TX 79758
Phone: (432) 563-0727
Fax: (432) 224-1038